Тема лекции: «Чугуны. Способы получения».
Слайд № 1
Способы получения чугуна.
В фильме мы подробно рассмотрели об устройстве и работе доменной печи , ее назначении. Для того чтобы закрепить информацию полученную из фильма, напомню вам основные моменты.
Слайд № 2
Доменная печь.
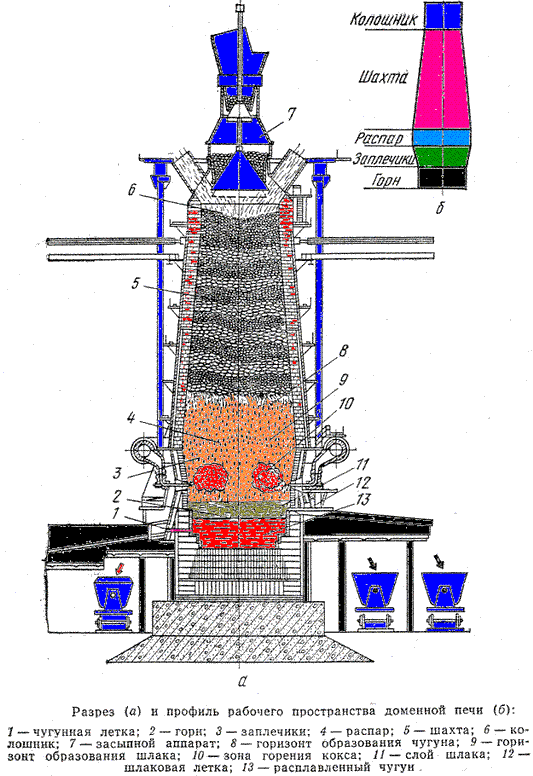
Рис.1 Устройство доменной печи
Основное назначение доменной печи – выплавка чугуна, для последующей переработки его в сталь для машиностроительного производства.
Справа вверху представлено упрощенное изображение домны или доменной печи.
Колошник - загрузочный бункер необходимый для загрузки шихты
Шахта - самая большая по высоте расширяющейся коническая часть, в которой происходят процессы нагрева материалов и восстановления железа из оксидов;
Распар - самая широкая цилиндрическая часть, в котором происходят процессы размягчения и плавления восстановленного железа
Заплечики - суживающаяся коническая часть, где образуется восстановительный газ
Горн - цилиндрическая часть, служащая для накопления жидких продуктов доменного процесса — чугуна и шлака.
По центру слайда подробный профильный разрез печи.
Высота современных доменных печей достигает 90 метров, объемом – 5500 м3 .
Слайд № 3 Схема доменного процесса.
Схема доменного процесса представлена на следующем слайде.
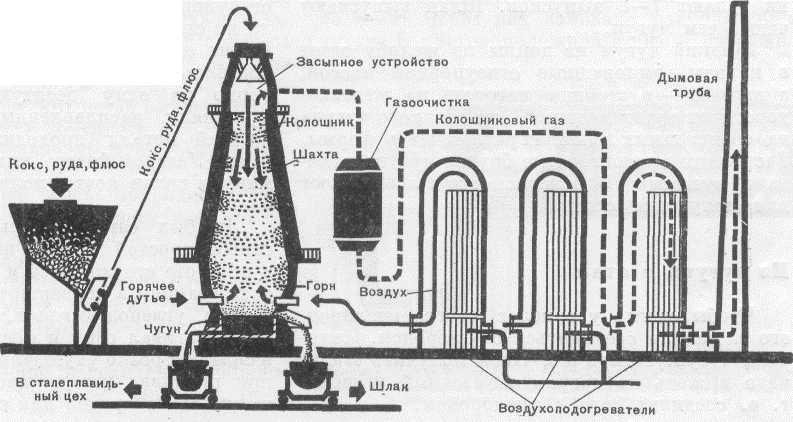
Рис.2 Схема доменного процесса
Слайд № 4 Диаграмма состояния.
На предыдущем занятии мы разбирали с вами диаграмму состояния для железоуглеродистых сплавов. В какой области диаграммы они распалагаются?
Следовательно, сплавы железа с углеродом, в которых углерода более 2,14 %, называют чугунами.
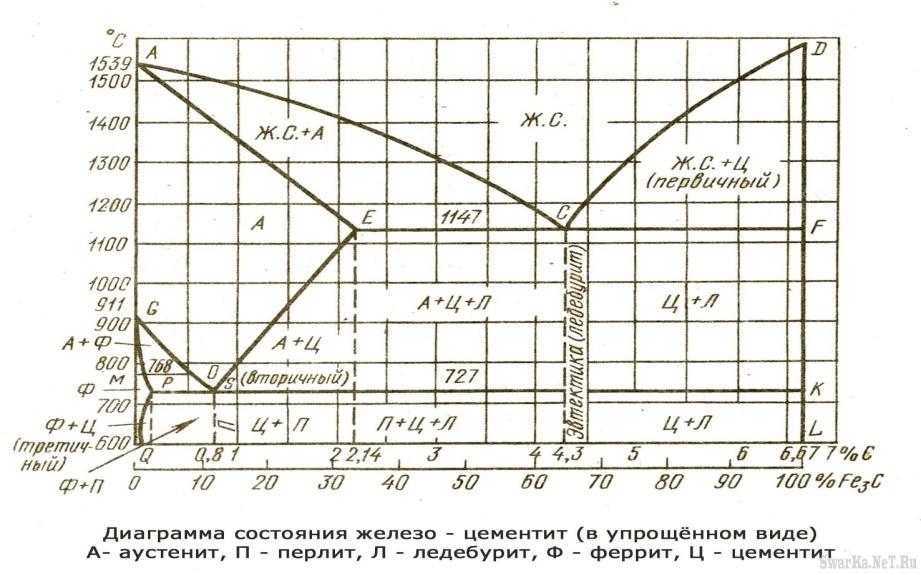
Рис.3 Диаграмма состояния
Слайд № 5. Структура чугуна.
Чугуны классифицируют по структурному признаку в зависимости от того, в каком состоянии находиться в них углерод (графит).На слайде представлена схема структуры графитовых включений: Металлическая матрица может быть ферритной, феррито-перлитной и перлитной. Формы графитовых включений могут быть : Пластинчатые , Хлопьевидные и Шаровидные.
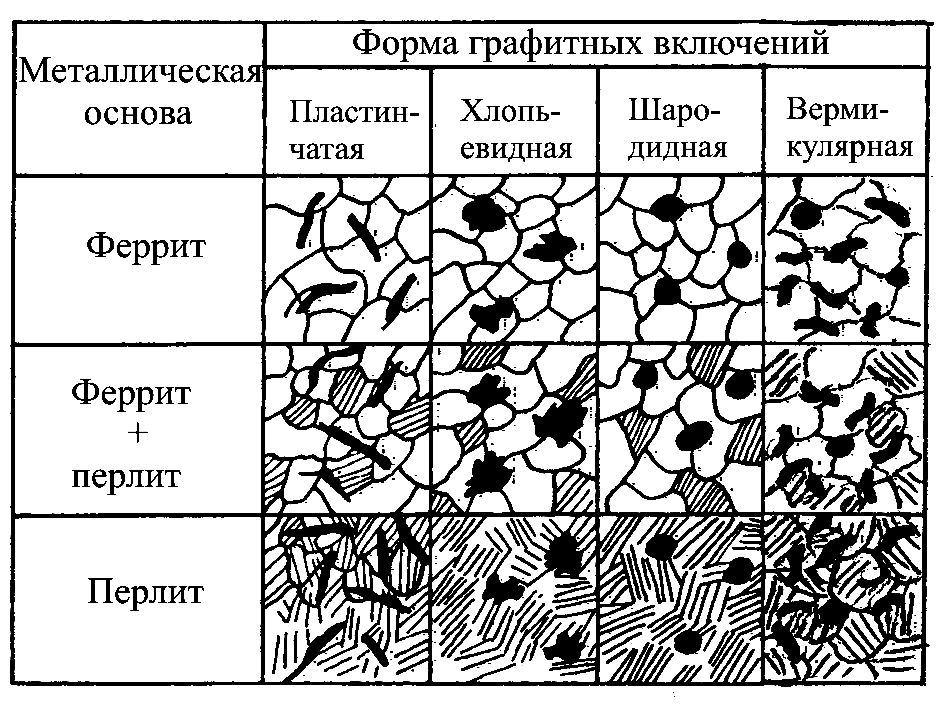
Рис 4. Форма графитовых включений
Слайд № 6. Виды чугунов.
Чугуны, в которых весь углерод или его часть находится в металлической матрице в свободном состоянии – в виде графита, подразделяются на три вида в зависимости от формы графитовых включений:
Серые чугуны. Форма графита пластинчатая, излом темно-серый.
Высокопрочные чугуны. Форма графита шаровидная.
Ковкие чугуны. Форма графита хлопьевидная.
Слайд№ 7. Обработка чугуна.
Процесс графитизации и структура чугуна определяется химическим составом и скоростью охлаждения. Обязательным компонентом чугуна является кремний, который вместе с углеродом способствует процессу графитизации. На процесс графитизации могут влиять два спсоба обработки жидкого чугуна:
Модифицирование металлов и сплавов это введение в расплавленные металлы и сплавы модификаторов, небольшие количества которых резко влияют на кристаллизацию, например вызывают формирование структурных составляющих в округлой или измельченной форме и способствуют их равномерному распределению в основной фазе. В результате модифицирования сплавы приобретают более тонкую структуру, что улучшает их механические свойства.
Легирование это введение в состав металлических сплавов легирующих элементов для придания сплавам определённых физических, химических или механических свойств.
Слайд № 8. Виды чугунов
Результатом различных способов обработки, различных химических составов является получение разных видов чугунов. Основными из которых считаются:
Серые чугуны обладают наименьшей прочностью. Пластинки графита можно рассматривать как трещины нарушающие целостность металла. Они имеют низкую прочность при растяжении, чем больше пластинки графита, тем меньше прочность чугуна.
Наличие свободного графита определяет преимущества чугуна перед сталью.
Лучшая обработка резаньем (стружка сыпучая, а не сливная)
Хорошие антифрикционные свойства (смазывающий эффект графита)
Высокие демпфирующие свойства (гашение вибрации)
Не чувствителен к поверхностным дефектам.
Серые чугуны получают отливкой.
Химический состав: С 2,4-3,8%; Si 1-4%$ Mn 1,25-1,4%; S 0.1-0.12%; P0.4-0.6%.
Сера и фосфор относятся к вредным примесям, поэтому за их % содержанием следят тщательно. Тем не менее фосфор придает чугуну повышенную жидкотекучесть, что широко используется в художественном литье : фосфора может быть до 1,6%.
Модифицируют серые чугуны 75%-м ферросилицием добавляя в расплав до 0,3-0,8%.
Легируют хромом, никелем, алюминием.
Маркировка: обозначают буквами СЧ и цифрами, которые указывают предел прочности при растяжении в кг/мм2 или МПа в соответствии с ГОСТ 1412-85.
Применяют серые чугуны для изготовления станин, поршней цилиндров, зубчатых колес.
Чем большее число присутствует в маркировке, тем более нагруженные детали изготавливают из данной марки чугуна. СЧ10,СЧ15-менее нагружаемые, СЧ30, СЧ35 – более нагружаемые детали.
Высокопрочные чугуны получают модифицированием чугунов перед заливкой магнием и церием. Под действием магния графит приобретает шаровидную форму. Такая форма обеспечивает высокие механические свойства.
Чугуны легируются с целью получения особых свойств: жаростойкости, антифрикционности, коррозионостойкости. Легирующими компонентами являются: никель, хром, молибден, титан, алюминий.
Ковкие чугуны получают из белых путем графитизирующего отжига (томления).
Слайд № 9. Отжиг белого чугуна на ковкий
Более подробно рассмотрим процесс получения ковкого чугуна.На рисунке 5представлена схема в виде диаграммы зависимости температурынх интервалов от времени выдержки. Схему отжтга можно разделить на несколько составляющих:
Нагрев
Выдержка при 950-970°С.
Ступенчатое охлаждение: первая ступень до 760° - вместе с печью, вторая ступень до 720 °С при выключенной печи.
Схема отжига белого чугуна на ковкий.
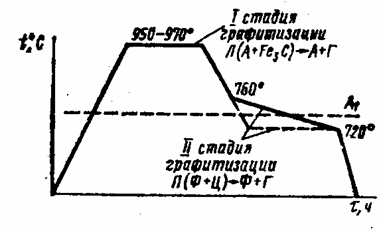
Рис. 5 схема отжига белого чугуна
1-я стадия-распад цементита входящего в состав ледебурита: Лед(А+Fe3C)→А +Граф и установление стабильного равновесия аустенит + графит. В результате распада цементита образуется хлопьевидный графит. Затем отливкимедленно охлаждают в течении 6-12 часов до t=720°С. При охлаждении происходит выделение из аустенита вторичного цементита и рост графитовых включений. При достижении t=720°С дают вторую длительную выдержку, при которой происходит распад цементита, входящего в перлит на феррит и графит: П(Ф+Ц)→Ф+Г.
2-я стадия длиться около 30 часов и после ее завершения структура чугуна состоит из графита и феррита. Излом у ковкого чугуна бархатно-черный из-за большого количества графита. Если вторую стадию не проводят, то получают ковкий чугун со структурой Г+П, излом такого чугуна светлый.
Такой отжиг занимает много времени 25+15+30 часов. Для ускорения отжига белого чугуна на ковкий применяют различные меры:
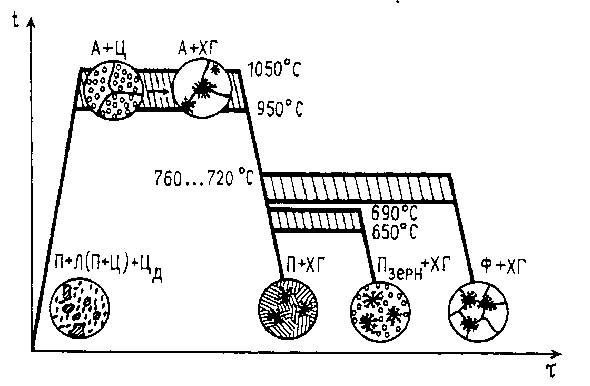
Рис.2 отжиг ковкого чугуна
Ковкий чугун модифицируют алюминием, бором, висмутом;
Повышают температуру нагрева перед разливкой;
Проводят перед отжигом закалку;
Повышают температуру первой стадии до 1080°С и т.д.
На рис.6 в виде изображений показаны структурные превращения происходящие в процессе отжига.
Пауза
Слайд № 10. Маркировка чугунов
Маркировка чугунов отличается от прочих достаточной простотой и минимальной информацией, которую можно получить из маркировки. Вся маркировка соответствует определенным ГОСТам, на каждый вид маркировки свой ГОСТ. Разберем маркировки основных видов чугунов.
Маркируют серые чугуны по ГОСТ 1412-85 буквами СЧ и цифрами, которые указывают предел прочности при растяжении в кг/мм2 или МПа,
СЧ 35 σв=35кг/мм2 или 350МПа .
Модифицированный серый чугун имеет высокую прочность, и все высшее марки чугуна получают методом модифицирования.
СЧ 28-48 расшифровывается: серый чугун с прочностью при растяжении 28 кгс/мм2(280 МПа ) и пределом прочности при изгибе 48 кгс/мм2 ( 480МПа).
Маркируют высокопрочные чугуны по ГОСТ 7293-85 буквами ВЧ и цифрами, первые две цифры после букв указывают предел прочности при растяжении в кг/мм2 или МПа, вторая цифра – относительное удлинение в %.
ВЧ60-2 σв=60кг/мм2 или 600МПа δ=2%.
Маркируют ковкие чугуны по ГОСТ 1215-79 буквами КЧ и цифрами, первые две цифры после букв указывают предел прочности при растяжении в кг/мм2 или МПа, вторая цифра – относительное удлинение в %.
КЧ45-6 σв=45кг/мм2 или 450МПа δ=6%.
В промышленности широко применяют изделия из легированных чугунов с особыми свойствами. Обычно их маркировка начинается с буквы, указывающей на область применения чугуна (жаростойкий, антифрикционный, износостойкий).
Например, по ГОСТ 1585–85 «Чугун антифрикционный для отливок» чугун маркируют буквами «АЧ» (антифрикционный чугун), затем указывают тип чугуна (С – серый с пластинчатым графитом, В – высокопрочный с шаровидным графитом, К – ковкий чугун с компактным графитом), далее число, обозначающее порядковый номер марки: АЧС–5.
Слайд № 11. Самостоятельная работа
Самостоятельная работа с маркировками чугунов.
Слайд № 12. Домашнее задание:
СЧ32-52 -
ИЧК–2 -
ВЧ 60 -2 -
СЧ44-64 -
КЧ 40-5 -
СЧ 15 -
АЧС–2 -
ВЧ45-0 -
ЖЧС-2 -
ВЧ50-1,5 -
Слайд № 13
Анкетирование
Слайд № 14
Заключение.
Влияние примесей на свойства чугуна.
УГЛЕРОД. Большая часть графита в чугуне находиться в виде чешуек графита, в связанном виде с железом – цементит, свободный графит, который частично разобщает металлическую основу и придает хрупкость. В сером чугуне углерода менее 4%, в прочных чугунах 2,8-3%. Отсюда следует что выделение графита в чугуне сопровождается увеличением объема, что понижает усадку до 1%. Кроме того при росте углерода чугун становиться более жидкотекучим, что улучшает литейные свойства и позволяет получать качественное тонкостенное литье.
КРЕМНИЙ. Кремний образует с железом силициды FeSi и Fe3Si2 . Таким образом рост доли кремний в чугуне приводит к снижению цементита Fe3C и как следствие улучшению обрабатываемости его режущим инструментом. Кремний повышает жидкотекучесть и снижает t плавления и объемное охлаждение чугуна. В сером чугуне кремния 0,75-3,75%.
МАРГАНЕЦ. Марганец повышает устойчивость Fe3C, способствует отбеливанию чугуна. Содержание марганца в сером чугуне до 1,3%. Марганец упрочняет чугун, парализует вредное влияние серы, повышает жидкотекучесть.
СЕРА. Сера - вредная примесь и содержание ее в сплаве не должно превышать 0,07%. Сера снижает жидкотекучесть чугуна, делает его густым.
ФОСФОР. Фосфор придает чугуну твердость и хрупкость, поэтому в чугунных деталях работающих под ударными нагрузками содержание фосфора должно быть менее 0,3%. Для деталей работающих на истирание твердость фосфора повышает износоустойчивость, поэтому при таких условиях эксплуатации допустимое содержание фосфора 0,7-0,8%. Фосфор снижает t плавления, повышает жидкотекучесть и снижает литейную усадку. Это позволяет получать из фосфористого чугуна отливки с чистой и гладкой поверхностью. Для художественного литья фосфора в чугуне может быть до 1,2%.
Легирование это введение в состав металлических сплавов легирующих элементов для придания сплавам определённых физических, химических или механических свойств. Легирование применялось ещё в глубокой древности (об этом свидетельствует исследование образцов холодного оружия, найденного при археологических раскопках). В России первые промышленные опыты легированием были проведены в 30-х гг. 19 века на Златоустовском заводе П.П. Аносовым, который разработал основы теории, и технологии выплавки легированной стали. Широкое промышленное значение легирование получило в годы 1-й мировой войны 1914—1918, когда для военных целей потребовалось большое количество хромоникелевой, молибденовой и др. сталей (для изготовления артиллерийских орудий, корабельной брони и т. д.).
Путём легирования создаются металлические сплавы с разнообразными свойствами, значительно отличающимися от свойств чистых металлов. От характера взаимодействия атомов различных элементов зависят кристаллическая структура и некоторые свойства (электрические, магнитные, тепловые) образующихся фаз. Легирование приводит к изменению условий равновесия фаз, выражающихся диаграммой состояния. Легирующие элементы в сочетании с основным элементом (растворителем) в зависимости от соотношения их атомных диаметров и электрохимических свойств образуют новые фазы — твёрдые растворы, промежуточные фазы, химические соединения. В присутствии легирующих элементов изменяются температуры перехода одной модификации в другую. Легирование меняет кинетику фазовых превращений. Легирующие элементы могут существенно понизить скорость распада твёрдых растворов, а в сталях — скорость распада аустенита, распада мартенсита при отпуске, коагуляции карбидов из-за понижения скорости диффузии атомов. (Эти обстоятельства широко используются в практике термической обработке металлов.) Изменение свойств сплавов в результате легирования обусловлено, кроме того, изменением формы, размеров и распределения структурных составляющих, изменением состава и состояния границ зёрен. Легирование может тормозить процессы рекристаллизации.
Легирование осуществляется, как правило, путём сплавления легирующих элементов с легируемым металлом (обычно в жидком виде).
Модифицирование металлов и сплавов это введение в расплавленные металлы и сплавы модификаторов, небольшие количества которых резко влияют на кристаллизацию, например вызывают формирование структурных составляющих в округлой или измельченной форме и способствуют их равномерному распределению в основной фазе. В результате модифицирования сплавы приобретают более тонкую структуру, что улучшает их механические свойства. Модифицирование применяется при производстве отливок из чугуна и силуминов - алюминиевых сплавов. Модифицирование отличается от микролегирования, при котором увеличение дозировки присадки приводит к обычному легированию (без явной границы между получаемыми эффектами). Примодифицирование увеличение дозировки присадки либо невозможно (из-за малой растворимости, летучести), либо неэффективно, либо вредно (перемодифицирование). Иногда при смешении двух различных расплавов наблюдается явление жидкого модифицирования. Эффект, подобный модифицированию, может быть получен при некоторых физических методах воздействия на жидкий металл, например при ультразвуковой обработке, наложении электромагнитного поля и др.
Модифицированный чугун имеет высокую прочность, и все высшее марки чугуна получают методом модифицирования: СЧ28-48, СЧ32-52, СЧ36-56, СЧ40-60, СЧ44-64.
Марка СЧ28-48 расшифровывается: серый чугун с прочностью при растяжении не менее 280 МПа (28 кгс/мм2) и пределом прочности при изгибе не менее 480МПа(48 кгс/мм2).
Модифицированный чугун содержит 2,6-3,2% углерода и 1,1-1,6 % кремния.